Cleaning Exterior Wood Surfaces
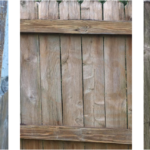
Cleaning Exterior Wood Surfaces As wood ages, mildew (mold) and algae begin to grow on the surface. This is a normal process; these organisms do not degrade the wood. They cannot break down the structural components of wood. They just live there. They feed off airborne contaminants, extractives, and oils in wood and in some … [Read more…]